A turnkey solution for Quesos Entrepinares
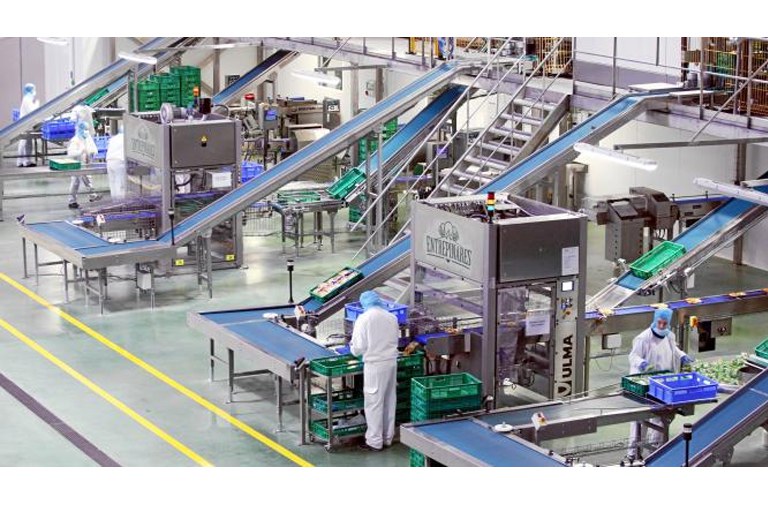
At the cheese curing and packaging plant run by Quesos Entrepinares, products from the client’s different factories are received and stored in order to be cured using a process managed by Ulma Handling. When the products have reached their optimum curing point they are removed from the warehouse, depalletised and at that point the installation developed by Ulma Packaging begins its work. The cheeses are sent to the packaging lines, where the packaging is performed using different technologies (thermoforming or vertical) depending on the type of cheese and its format: whole cheeses, wedges, sliced, shredded, etc. Quality control, box packing and palletizing are performed at the exit from packaging. The final part of the process again falls to Ulma Handling: the finished pallets are stored in two smart warehouses until their dispatch.
Entrepinares, an inter-supplier to Mercadona, is the largest producer of cheese in Spain. With a production of 45 million kilograms of cheese a year and a range containing 90 SKUs, it has entrusted ULMA with the full integration of the system at its new plant, with about 30 packaging lines and a production of approximately 1,200 boxes/hour.
One of the great challenges at the installation was to implement a new fully automatic plant, including the transfer of the packaging lines from the previous plant, without any interruptions in the client’s operations. In addition, it was necessary to transfer the whole process of storage and packaging of cheese with the client’s computer system so that the plant could automatically perform warehouse management and order planning operations, and synchronise its commissioning with production so the client did not suffer any interruptions in its service.
ULMA Packaging contributed a full integration of the system together with Ulma Handling to offer the client a turnkey solution. The client only had to deal with making cheese, while the logistics and packaging were fully managed by ULMA. The installation was a complete success and the plant has been running at full capacity for four years, with higher productivity levels than those contracted.