Barry Callebaut, comprehensive response to container handling needs
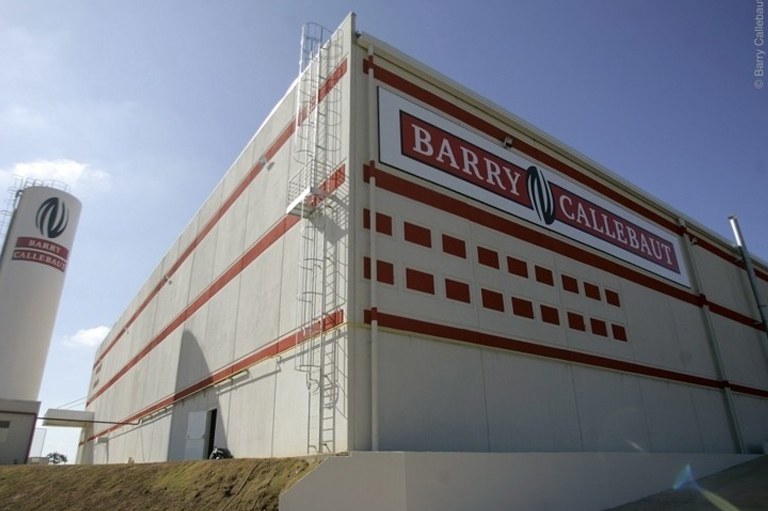
The project involved the integration of 3 bagging and box packing lines with a handling system for bags containing granulated chocolate, including the automatic box packing of the bag using an automatic cardboard forming and closing machine. The installation also has a control process with a bag weigher, security barcode reader, box labelling and bar code reader control.
The size of the client - Barry Callebaut is the world’s leading producer of chocolate base and cocoa for manufacturers of products using chocolate and its derivatives and direct sale to catering - and the complexity of the confectionery, chocolate and derivatives industry, since it is a granulated product, have been two factors that have influenced the installation, requiring the handling of a preformed bag containing product. The dimensions of the bag also vary with the weights, ranging from 1 kg: 290x160x85 mm, 1.5 kg: 320x190x90 mm, 2.5 kg: 330x215x120 mm and 5 kg: 425x235x120 mm.
ULMA Packaging is involved in the process from the receipt of the prefabricated bag. The bagged and closed product is received and channelled on plastic conveyor belts, with the product being handled by a tracking robot. The cardboard is supplied automatically to the handling area using automatic forming machines.
Specifically, one of the main challenges presented by this project was to solve the handling by a robot of bags from the range of defined sizes and weights, considering that the bag is a pillow bag containing product that can be distributed variably, at a maximum speed of 30 bags/min. This was resolved through handling it with a gripper made up of pneumatic suction cups, and also a turn performed by the robot at the speed described.
The client’s needs included achieving the handling of containers in a controlled manner, positioning of bags inside the box in an orderly manner to facilitate the entry of the number of bags required per box and being able to perform an exhaustive control of the product, including information on the product and box to achieve accurate traceability, in addition to meeting delivery dates.
A detailed study allowed the correct definition of the elements to be used in the installation, such as the choice of robot and its characteristics, the design of transport equipment, etc. Since there are 3 equal lines, the logical process led to the addressing of a first box packing line so the other two could be designed and assembled in a simpler way, after having resolved the difficulties seen in the first assembly. The complication came especially during the commissioning process, since it was a complete line containing several key elements.
The proposal of a turnkey installation in which we undertook to handle all the peripheral elements meant that in ULMA Packaging the client found a company which provided a comprehensive response to its needs. The proposal type with a delta robot, and the versatility and flexibility that it offered was more convincing than other solutions presented, with handling tests being performed in the proposal stage for which the client was grateful.
The end result has been very positive, achieving the handling of all the products at the required speed and forming defined patterns, maintaining a stable solution that is constantly working