Thermoforming - the ideal product packaging solution
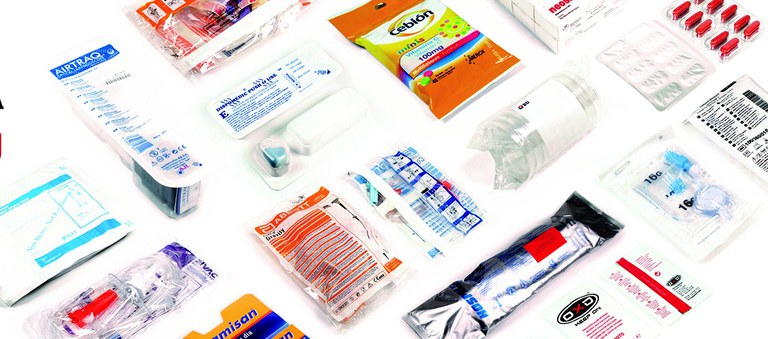
Pharmaceutical and medical manufacturers are under increasing pressure to achieve cost savings and improve sustainability, without compromising on all-important product safety. The latest thermoform packaging technology can provide a transformative solution to these concerns, and lead to savings at all stages of the packaging process. With that in mind, Alastair Cook, Product Manager at ULMA Packaging, explains the thermoform process and how companies in the pharmaceutical and medical sector could stand to benefit.
The medical and pharmaceutical industries require fully reliable packaging that offers the maximum possible protection for products designed to care for and preserve the health of people. Consequently, companies in these industries require packaging solutions that meet the strictest regulations required by these sectors.
These criteria include ISO 11607 for the packaging of medical products, with ISO 15378 and National Pharmaceutical Association standards applying to the packaging of medicinal products including pharmaceuticals. These extremely stringent regulations are frequently updated as part of ongoing efforts to provide a guaranteed solution that protects both the product and the patient using them.
Rigorous standards
Yet, as well as remaining in line with ISO 11607:2019 and ISO 15378 and NPA standards, further legislation has recently been introduced to tighten product safety in the supply chain. The new Falsified Medicines Directive (FMD) was introduced by the European Union in February this year, and the UK Government has confirmed it will continue to be in effect regardless of Brexit.
Designed to improve protection and preserve the tough sterilisation conditions in the healthcare sector, the legislation sets out two mandatory safety demands on packs of medical products. These demands include a unique identifier barcode to ensure full traceability, and tamper evident features to assure patients that their medicines have not been interfered with.
Many manufacturers of pharmaceutical and medical products go beyond even the heightened scrutiny specified in current legislation to provide quality control assurance, achieving compliance with regulations such as Part 11 of Title 21 of the Code of Federal Regulations, otherwise known as Title 21 CFR Part 11, or Part 11 for short. Though part of the USA’s Food and Drug Administration (FDA) regulations, a number of UK organisations have implemented practices set down in Part 11. Its criteria look to ensure electronic records in the healthcare, biotech and biologic fields can be considered as trustworthy as equivalent paper records. Put into practice, this translates into implementing controls such as audits, system validations, audit trails, electronic signatures and the documentation for software and systems involved in processing electronic data.
Best possible practice
For medical and pharmaceutical manufacturers, Part 11 can be felt at the product packaging stage. By keeping hold of important control system data, the manufacturer can identify a number of metrics, including each machine packaging cycle, the cycle number, the parameters being monitored, and even the identity of the machine operator. This extremely forensic process further bolsters quality control, enabling close evaluation of machine data to enforce best possible practice. Again, while optional, Part 11 further highlights just how important the avoidance of spoiled products is in the pharmaceutical and medical sectors.
So, when specifying an appropriate product packaging solution in such heavily-regulated sectors, it is vital that the integrity of packaged pharmaceutical products and medical devices is not compromised. Though factors that could result in product spoilage should be a concern no matter the manufacturer’s industry, maintaining a contaminant-free packaging process is the highest possible priority to pharmaceutical and medical manufacturers.
Indeed, the risk of contamination in these sectors cannot be overstated, as it can impair the packaging process, and any adverse effects could lead to potential fines, reputational damage, and, most seriously, jeopardise consumer health.
Suitable packaging solutions
A number of materials can be used in the packaging of such products, including plastic films, medical-grade paper, synthetic materials such as Tyvek® flash spun high-density polyethylene, or aluminized materials, such as steel. Though these materials provide necessary protection for packaged products, how they are utilised can increase their effectiveness. As such, specifying the appropriate machinery required to package such sensitive products is one of the most important decisions a pharmaceutical or medical manufacturer can make.
Of the wide variety of packaging technologies and lines available, thermoforming stands out as ideally suited to the demands of mass medical device and pharmaceutical product packaging. Naturally versatile, robust and reliable, thermoform machines can use a plethora of both rigid and flexible packaging materials to create dependable, protective packaging.
Thermoforming process
Thermoform machines for the pharmaceutical and medical sector produce trays on a horizontal packaging line, using two film coils normally made of different rollstock materials. Both materials are unwound from their respective reels and fed through a pre-heating station consisting of an upper and lower plate, softening the material to the extent that it becomes more pliable.
The bottom film is heated and negatively formed into a cavity with the use of vacuum or occasionally highly-filtered compressed air, which is then cooled so the plastic becomes rigid when removed from the mould. For difficult shapes, such as those required by blister packaging where the cavity shape is larger than a small tablet or medical device, a ‘plug assist’ feature partially pushes the plastic down into the cavity to assure a more even and uniform wall distribution.
After this cavity is created, the product is loaded via automated product filling. The top film layer is then rolled over the mould and heated, creating a hermetic, airtight seal between the product and the surrounding environment. This thermoform fill seal process, which all takes place on the same equipment, provides an extremely effective level of protection against external contaminants or tampering. As well as being extremely durable, the high-quality seal also keeps the packaging product in place, reducing the risk of damage during transportation.
The packaged product is then cut into its final shape from a larger tray and ejected from the thermoforming machine. These finished pharmaceuticals or medical devices are then able to be sterilised via steam-heat treatments, radiation or gases such as ethylene oxide, without compromising the packaging integrity mandated by pharmaceutical and packaging manufacturers.
Further security
Thermoforming machinery provided by leading packaging machinery suppliers can provide fixed and variable data printing and labelling before or after sealing. This can also take place before the cutting stages to ensure the finished product is in accordance with the relevant standard. As a result, all stages of the packaging process can be closely monitored to assure pharmaceutical and medical manufacturers of the highest possible product standards. The modular design of thermoforming machines also allows for monitors to be added at all parts of the packaging process, enforcing consistency.
Monitored parameters include forming time, homogenous temperature across the packaging, and guaranteeing that the forming process remains at optimum temperature. If there is a deviation from the criteria, any faulty product can be sealed and ejected from the packaging line without coding.
Due to their adaptability, combined with the availability of highly accurate sensor and measuring apparatus, thermoforming machines are well-placed to meet the rigorous demands required by sector legislation. This includes meeting standards set out in qualification systems – including installation qualification, operational qualification and performance qualification – that make up factory acceptance tests.
Considering sustainability
Outside of stringent performance standards, a key concern for manufacturers in the medical and pharmaceutical sectors should be sustainability. The ‘Blue Planet’ effect has rightly made the use of plastic a hot topic in the news agenda, and any stakeholders looking to invest in new packaging lines will find themselves taking it into account. Indeed, with consumers attitudes shifting and the packaging industry accounting for 40% of plastic processed every year, it is clear sustainable solutions that minimise waste must be found. These changing and highly demanding sets of circumstances are affecting all industries, including pharmaceutical and medical product manufacturing.
So, with experts calculating that demand of plastic packaging demand will double in the next 20 years, pharmaceutical and medical manufacturers need to be aware of the growing trend toward sustainable materials. But in a marketplace driven by product security, it is key that any sustainable solution can still deliver the hermetic seal required to minimise contamination risks.
Thermoforming already enjoys a sterling reputation as an energy-efficient and environmentally friendly packaging method. Using thermoform technology, organisations can therefore implement more sustainable operations through creating a process that is truly efficient from the top down. As a result, businesses can therefore realise financial and productivity benefits, securing a competitive edge while enhancing their green credentials, and without sacrificing product integrity.
From manufacture all the way down the supply chain, thermoforming can therefore provide a way to reduce environmental impact while still providing the hermetic seal which is so vital to packaging in these sectors. Changes such as these could also give manufacturers a competitive edge, chiming with public sentiment over single-use plastic while also identifying areas in which efficiencies can be made without compromising all-important hygiene criteria surrounding pharmaceutical and medical product packaging.
Reducing packaging processor waste
A good example of where these efficiencies can be found is at the processing stage. Though all packaging processors will accrue some degree of loss from raw material, if measured out over an entire production period, this small by product can become quite a significant amount of waste. This is further exacerbated by the costs involved with removing the waste from the manufacturers’ premises, which further impacts the financial bottom line.
However, packaging machinery technology has progressed to address this issue. Certain packaging solution manufacturers have developed reduced scrap machine options that are compatible with thermoforming solutions, helping manufacturers markedly reduce material waste and disposal costs. These machines use a narrower reel of film than standard, allowing for pronounced waste reduction, and, when combined with machine automation capabilities, enhanced productivity
Further efficiency
Alongside allowing for a reduction in waste materials, the thermoforming method can offer pharmaceutical and medical manufacturers an opportunity to see how the packing format can be integrated into manufacturing processes. Though some may prefer to queue the product into the process, this can be very inefficient – by contrast, thermoforming can enact positive change throughout the production line, improving precision and optimising each step involved.
Due to the very nature of thermoforming, pharmaceutical and medical manufacturers are able to make even more pronounced cost savings while realising both sustainability and efficiency benefits. This is because the finished package can be created on demand, and arrives fully-formed on the machine from a roll of stock material.
By offering a one-stop packaging solution, with no further transportation of products to the manufacturing facility required, companies can therefore make pronounced cost savings around the transportation of packaging materials, while reducing their carbon footprint. Situating all packaging processes in one place also provides an opportunity for manufacturers to use lighter gauge materials, providing excellent product protection alongside further savings.
In conclusion, reducing contaminants in the packaging process is important no matter the industry, but it is absolutely vital within the pharmaceutical and medical sectors. In such sensitive environments, thermoform packaging technology represents an ideal solution, allowing manufacturers to guarantee product integrity while also achieving cost savings and make strides toward sustainability.
For more information, please visit our website.
Alastair Cook Bio
Alastair Cook is a Product Manager at ULMA Packaging UK. He has worked for the company since its formation 18 years ago, and has been integral to the technical development of a host of ULMA packaging machinery during this time. Alastair is an expert in the packaging industry, and has utilised his broad knowledge in the development of ULMA’s range of vertical and horizontal packaging machines for produce resealable packs. He specialises in the fields of thermoforming and tray sealers, and has taken an active role in the development of recyclable material options for ULMA’s thermoforming range.