ULMA Packaging, expertise in advanced sealing technologies for flexible materials
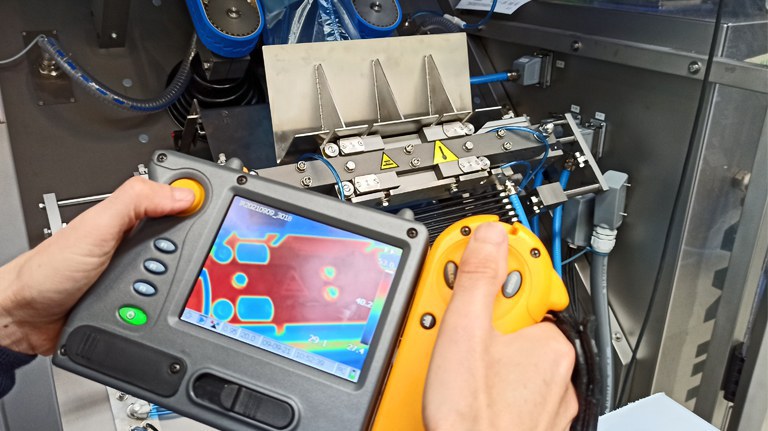
Through our in-house innovation centre, ULMA Packaging Technological Center, and more specifically, the Advanced Sealing Technologies Division, we have developed systems that allow us to offer the option best suited to the packaging material, the product to be packaged and the production requirements of each customer.
Erika Revalo, an engineer specialising in films and sealing, works in the Advanced Sealing Technologies Area, and according to her, "our customers are constantly sending us new materials to test, and they truly value our advice on sealing technology and on configuring the most suitable packaging machine according to their needs and requirements".
Erika points to aspects related to other areas of activity in her department: "We are firmly committed to sustainable materials, so we work with film suppliers in order to develop new products that also ensure a suitable level of sealability. Research into developing new sealing technologies also takes up a large part of our time, it is one of the other areas where we work very hard in order to equip our machines with the most advanced sealing systems."
Sealing technologies
BETTER-SEALTM
This sealing technology is among the most innovative developments in the cross-company #ULMAweCare sustainability plan, focused on achieving a circular economy. More specifically, BETTER-SEAL is a new technology that ensures stable and precise temperatures of the sealing elements in the machines, allowing the option of working seamlessly with new materials in sustainable and recyclable packaging solutions.
SEALFLEXTM
A system aimed at the frozen products sector, which streamlines and simplifies sealing jaw changes when switching packaging material. Avoiding having to change the entire jaw means that changeover times are kept to a minimum, thus optimising maintenance stoppages and maximising packaging machine uptime.
JAW TOOTHING
The expertise we have gained through extensive experience means we can offer each customer the optimal toothing profile, ensuring a perfect seal for every package. This area of work has a significant impact on optimal seal quality, and therefore a direct effect on the airtightness of the package, allowing us to guarantee food safety and food preservation.
PAPER SEALING
Another of our latest innovations has come from developing paper-based packaging solutions. The technologies we employ allow us to adapt a large number of our machines to use paper, guaranteeing the same sealing quality on the packaging as when using traditional materials.
COLD SEALING
The packaging requirements, either due to the characteristics of the product to be packaged and/or the productivity levels to be achieved, can make it necessary to use non-heat sealable films.
Our extensive experience in this type of application means we can offer solutions to customers requiring cold sealing that avoid damaging the product and guarantee a perfect seal.
IMPULSE SEALING
This technology is used to seal packaging materials that generate waste in conventional systems, since such waste has a direct impact on seal quality.
Our know-how in regards to this sealing technology allows customers to reduce maintenance downtimes and thus increase OEE levels.
ULTRASONIC SEALING
Ultrasonic sealing technology ensures the fusion of the inner surfaces of the films to be sealed by the vibration generated by the sonotrode.
This technology has a series of benefits whenever the surfaces to be sealed may be contaminated by the product to be packaged (e.g. vegetables, products with liquids or fats, etc.), or by materials that pose sealing difficulties as the outer surface in contact with the sealing elements does not heat up.
Another feature of this system is its ability to increase packaging production thanks to sealing times being kept to a minimum, making it a very suitable sealing technology for applications that require high-speed packaging processes for materials that are complex to seal.
Working with flexible film suppliers
Working with film suppliers is a key aspect that we keep very much in mind. That is why we have been working for decades with a wide range of packaging material suppliers, with whom we have gained sufficient know-how and experience in order to always recommend the best option available on the market.
This close collaboration means that we are at the technological forefront in terms of knowledge of new materials, allowing us to offer our customers comprehensive solutions.
Sealing element treatments and coatings
Knowledge of specific treatments and coatings for sealing elements is another of our areas of technological expertise.
At ULMA Packaging, we know that all treatments and coatings applied to jaws, rollers, plates, etc., play a key role in sealing performance.
That is why we apply the ideal treatment and/or coating for the packaging material to be used by the packaging machine, guaranteeing sealing stability over time.
At ULMA, we are more than happy to advise you on the sealing technologies required by your packaging machine, thus ensuring that your product is packaged with the highest level of safety, preserving its characteristics throughout its shelf life until it reaches the end customer.
Please do not hesitate to get in touch through the contact form if you have any queries.