La Anónima chooses ULMA Packaging for the vacuum packing of meat with the Flow-vac® system
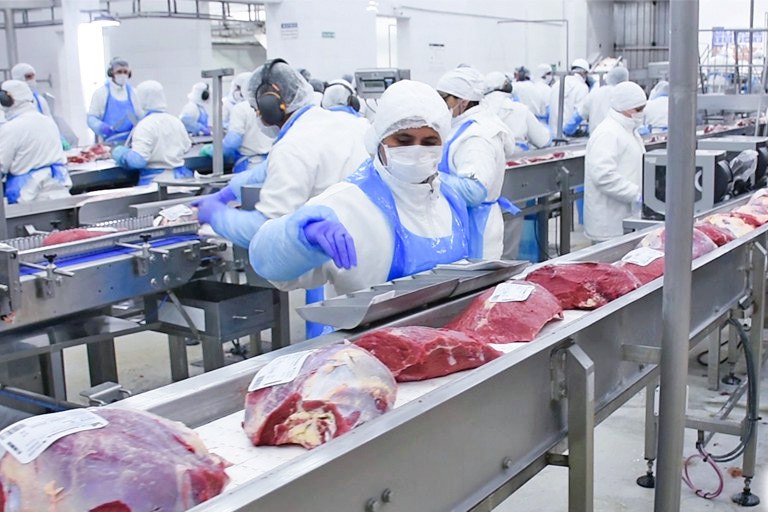
La Anónima, which has been operating continuously for over a century, is one of the largest supermarket chains in the Patagonia and central inland regions of Argentina. It is the industry's fourth largest company nationwide and the second largest Argentinian-owned company. It has over 150 stores, which are supplied from its two cold storage facilities, the Frigorifico La Anonima, in the city of Salto, Buenos Aires (Argentina), and the Frigorifico Pampa Natural, located in Speluzzi, La Pampa (Argentina). Both plants process approximately 20,000 heads of Angus cattle every month.
When undertaking this installation, ULMA Packaging's main challenge was to improve the production efficiency of a traditional working method in South America, i.e. the manual packaging of meat cuts, thus achieving better productivity. This was a huge challenge because we needed to redesign the layout of a very small space in very little time, as it was necessary to get the installation up and running during the cold storage facility's very short period of downtime, in the summer holidays. It also involved major changes to the process, moving from traditional packaging to automatic packaging, with a highly moist product, where a vacuum leakage error could affect huge quantities of meat. The customer needed to automate the processes to improve its output in tons and reduce the amount of labour, which adds no value to its process. La Anonima has grown gradually in recent years; over the last three years it has gone from being allocated 1,800 tons of the Hilton quota - an export quota for high-quality and high-value boneless beef that is set by the European Union for producing and exporting countries - to the current 2,300 tons, and the new facility must meet the needs of a customer who is extremely demanding regarding output, deadlines and quality.
At the start of 2018, two lines were installed in Frigorifico La Anonima in Buenos Aires: a FV 35 and a FV 55, both with automatic loading to Sealed Air VS95 vacuum chambers. The design was defined by ULMA Packaging's technical department for the packaging of beef cuts, intended for the domestic and foreign markets (EU, China, Russia and Brazil).
These first two lines were defined during the initial stage and, following the success of the design, the third line was defined in the last three months of 2018, consisting of a second FV 55 with automatic loading to vacuum chambers.
The installation has a butchering facility, spread over two floors. On the top floor there is a forequarter and hindquarter deboning room, a cutting room and the primary packaging area, which is divided into the two Flow-vac® FV 35 and FV 55 lines, each for different sizes of cuts, both with automatic loading to a VS95 chamber and with their respective heat shrink tunnels.
There is also a separate line for trimmings, which is fed into the Marel TMS, which manages beef trimmings according to their fat content. The secondary packaging area is on the second floor, with a meat-cutting carousel system to ensure an even workflow for the workers, metal detectors and box-handling equipment. The production capacity is 3000 quarters over two 9-hour shifts, with a total of 90 tons of cuts being vacuum packed by ULMA's two Flow-vac® lines and 40 tons of beef trimmings being fed into the Marel TMS, making a total of 130 tons per day.
TMS MAREL (Trimming Management System |
Primary |
Flow-vac® FV 35 |
Flow-vac® FV 55 |
2 positioners |
2 Cryovac VS 95 |
2 water heat shrink tunnels |
Secondary |
Cutting carousel system |
Metal detector |
Box-handling systems |
ULMA Packaging brought over 18 years of experience in the global market to this demanding project with the installation of the Flow-vac® system, converting a traditional packaging facility into an automatic packaging plant. This was essential for improving the hygiene of the process and it led to a qualitative leap in the way the product is presented by standardising package sizes, reducing stocks and decreasing the consumption of plastic.
The result of the project can be classified as excellent, as we met all of the objectives that were set, improving presentation for certain markets such as China, which is highly demanding with regard to packaging. The customer's satisfaction with this installation adds yet another success to the long list of automation projects carried out by ULMA Packaging.